I know what you are thinking, the meme with 4 to 6 squares showing "what my family thinks I do", "what my friends think I do", "what my cat thinks I do", "what I think I do"...
And, the "what do I do square" is something like excel spreadsheets... For the college engineering majors reading this and thinking about dropping out and starting an NFT, actually it might be worthwhile. I hold my neutral stance that NFTs and Crypto are useful in providing value to society in terms of transaction and copyright decentralization, but can also become dangerously speculative.
Okay back to what do I do as a NASA-JPL Mechanical Engineer. This isn't a New York Times edition, so don't expect too much, I don't do anything important anyways.
Yes, I do use spreadsheets.
Anyways, top level summary:
I'm a mechanical packaging engineer and I package tofu for the Mars Sample Return Lander (Not the orbiter). My JPL colleagues might have aversions about their sensitive electronics being called tofu. But they are delicate, compared to say a metallic or composite structure.
Mars Sample Return is the other NASA flagship mission alongside the Artemis program, the finale of the endeavor that started with the M2020 Perseverance rover and Ingenuity helicopter (pictured below):
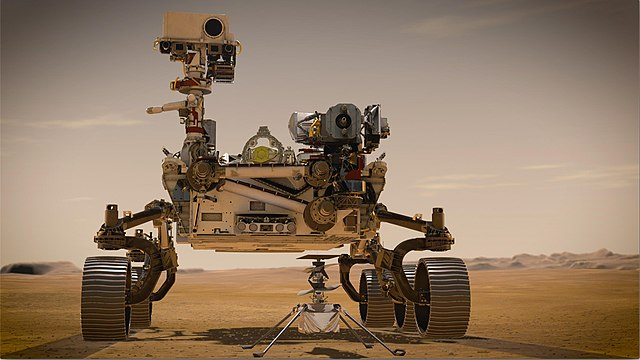
Image Source: https://commons.wikimedia.org/wiki/File:PIA23962-Mars2020-Rover%26Helicopter-20200714.jpg
License: Public Domain
The aim of the Mars Sample Return mission is to bring back Martian samples for analysis and examination on earth. We can only pack so much equipment into the Perseverance rover and the rovers before him/her to do rudimentary analysis. We will likely be able to find out a lot more about the red planet by bringing samples back to earth.
The Perseverance rover has been collecting soil and atmospheric samples of the red planet and has been dropping them at several locations as well as storing them in its belly. In the event that the Perseverance rover is non-operational, the samples that were left in specific depots on Mars would serve as a back-up cache. By the end of this decade, a Mars Sample Return Lander carrying with it a two stage rocket would land on Mars. In the plan A scenario, the Perseverance rover would drive to the lander and the lander would grab samples from the rover's belly. In the plan B scenario, the lander would deploy two helicopters similar to Ingenuity to fetch the samples at backup locations. The samples would be inserted into a the payload section of a two stage solid rocket. This rocket would launch from the lander and insert the payload into Martian orbit. An orbiter orbiting Mars (part of a separate launch from earth), would intercept the samples payload. This orbiter will detach major components while in Mars orbit to help reach escape velocity (conservation of momentum and F=ma at work). What remains of the orbiter will travel back to earth, and before reaching earth detach from the return payload, sending the payload on a precise trajectory back to earth and crash land on earth. The orbiter portion will perform maneuvers to enter an orbit around the sun, never to be seen again.
Animation of above sequence: https://www.youtube.com/watch?v=t9G36CDLzIg
Courtesy NASA/JPL-Caltech
Back to what I do for all this. Remember the tofu? The electronics usually need protection from the sun, from the horrid vibrations at launch, breaking the sound barrier, and from the extreme temperature swings of Mars as well as the generally frigid temperatures between the planets. A vacuum environment also means certain materials cannot be used and precaution of weird out-gassing and metallic whisker forming behaviors must be taken. I design and assist in the testing of mechanical structures that would protect and support the electronics. Sometimes, if a single piece of equipment goes down, the whole mission can be a failure. Before the design is tested, I usually do structural and thermal analysis to get a ball-park sense of if the design is going to work. Then I support the prototype build and testing. Testing is usually done in thermal-vac chambers to simulate the space environment. The launch environment and separation events are usually simulated with vibration tests on shaker tables and shock tests on shock beams. We would make design changes if something didn't work out and produce the next iteration.
In my role I wear multiple hats, sometimes I would be doing CAD (computer-aided design) 3D modeling, GD&T (geometric dimensioning and tolerancing) 2D drawings; sometimes I would do finite element analyses; and sometimes I would actually get to hold hardware and inspect it especially if it was a first build. This work all flows up and get integrated into the spacecraft sub-assembly level, and tests and analysis are done at that level by my dear colleges.
This all culminates into a single spacecraft level, and that gets shipped to Cape Canaveral!
7/17/24 Update:
Now I do a lot more mechanical mechanisms. Remember that Ingenuity helicopter that sadly broke its wings earlier in January of 2024, I now work with the team that put the first flying thing on mars. Now we are developing the next generation of helicopters. I work on a lot of moving mechanisms nowadays, but I still do tofu protection work also. It has been really dynamic. Mars entry and descent is very dynamic, so the really smart guys will do the CFD (computational fluid dynamics, i.e. Navier-Stokes and other unsolvable equations) and feed me the loads on say a helicopter and I would develop hardware to the environmental conditions plus some factor of safety. These can be flight separation mechanisms, structures, actuator devices, rocket motors etc.
Kommentare